Nylon Gear for Textile Machinery
Nylon gears are used in textile machinery to transmit power while protecting metal gears. Nylon gears have self-lubricating properties, work more quietly, have lower production costs, longer service life, and lower maintenance costs.
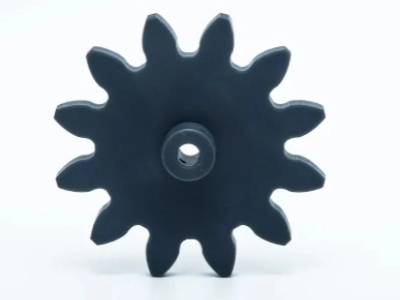
Technical Information
In the modern textile industry, high efficiency, low energy consumption, and stability of equipment operation have become the core concerns. As an important component in the mechanical transmission system, the performance of the gear directly affects the operating accuracy and service life of the equipment. Compared with traditional metal gears, high-performance nylon gears are being used more and more widely in textile machinery due to their excellent physical and chemical properties.
The role of nylon gears in textile machinery
Textile equipment runs at a high speed and has a long continuous working time, which puts high requirements on the transmission accuracy, wear resistance, quietness, and load-bearing capacity of gears. Nylon gears have significant advantages in these aspects and are often used in multiple core transmission systems such as spinning machines, twisting machines, looms, and winding machines.
Nylon gear classification
Nylon helical gears
Nylon pinion gears
Nylon plastic gears
Nylon sprocket gears
Advantages of high-performance nylon gears
High strength and wear resistance
Nylon material has excellent mechanical strength and self-lubrication, is suitable for high-frequency meshing operations, and can still maintain a good tooth surface state after long-term use.
Low-noise transmission
Nylon material itself has good shock absorption performance, which can effectively reduce the running noise, and is particularly suitable for textile workshop environments that have requirements for running noise.
Good corrosion resistance, oil resistance and moisture resistance
The humidity in textile workshops is high, and nylon gears have excellent environmental resistance, are not easy to rust or age, and are suitable for complex working conditions.
Reduce equipment load
Compared with metal gears, nylon material is lighter, which helps to reduce the weight of the whole machine, reduce energy consumption, and improve operating efficiency.
Flexible processing and support customization
Nylon gears can be precisely processed according to the structural dimensions of different textile equipment to meet various special transmission requirements.
Application scenarios
High-speed spinning machine: stable transmission and quiet operation are required. Nylon gears can achieve low friction and low vibration operation in such equipment.
Automatic winding equipment: high transmission accuracy requirements, nylon gears ensure uniformity of tension control and improve yarn quality.
Twisting machine, warping machine, etc.: suitable for transmission systems with medium load capacity and stable operation rhythm.
With the development of intelligence and high-speed textile equipment, higher performance standards are proposed for components. High-performance nylon gears have become an ideal transmission solution for modern textile machinery with their excellent wear resistance, low noise, light weight, and high precision. Whether pursuing stable operation or reducing maintenance costs, nylon gears can bring significant improvements to textile equipment.
You have questions, we have answers. Contact us today. Our skilled customer service specialists can help you make the right choice in polyurethane applications.
Nylon Gear for Nuclear Power Plants
none